1
00:00:00,400 --> 00:00:06,433
Hello everyone, today we are going to learn a typical single PWM controller workflow
2
00:00:07,366 --> 00:00:12,733
Single PWM controller refers to the chip that can only control 1 PWM output,
3
00:00:13,500 --> 00:00:16,500
this is called single PWM controller
4
00:00:17,166 --> 00:00:21,466
For example, this chip model is RT8209,
5
00:00:21,633 --> 00:00:23,366
and it's made by Richtek
6
00:00:24,666 --> 00:00:32,800
There are three models: RT8209A, RT8209B, RT8209C
7
00:00:33,333 --> 00:00:35,233
They have different package modes
8
00:00:36,300 --> 00:00:41,466
RT8209A has 16 pins and four pins on one side,
9
00:00:42,300 --> 00:00:45,433
and RT8209B has 14 pins
10
00:00:46,066 --> 00:00:48,766
Both of these are QFN packages
11
00:00:49,100 --> 00:00:54,166
However, RT8209C is TSSOP package
12
00:00:54,733 --> 00:00:57,666
Next, let's take a look at how the chip works
13
00:00:58,633 --> 00:01:02,033
For this chip to work, it must first meet the power supply
14
00:01:02,533 --> 00:01:06,300
Here, the VDDP and VDD pins are its power pins
15
00:01:07,666 --> 00:01:12,366
After the power supply is satisfied, the on signal must be satisfied
16
00:01:13,566 --> 00:01:16,766
Here, EN is a high level enable signal
17
00:01:17,333 --> 00:01:19,833
When it gets power and enable signal
18
00:01:20,033 --> 00:01:24,000
It will output the upper tube drive and lower tube drive pulses
19
00:01:24,166 --> 00:01:29,266
according to the current set by CS pin and the frequency set by TON pin,
20
00:01:29,266 --> 00:01:35,366
to control the upper and lower tube conduction in turn, and generate a continuous power supply output
21
00:01:37,933 --> 00:01:41,600
FB pin is used to detect and adjust its output voltage,
22
00:01:42,100 --> 00:01:47,200
VOUT pin is used to detect whether the output voltage at the back end of the inductor
23
00:01:47,200 --> 00:01:49,500
is overvoltage or undervoltage
24
00:01:54,100 --> 00:01:57,100
When the output voltage is detected to be normal,
25
00:01:57,866 --> 00:02:00,233
the PG signal output is delayed
26
00:02:03,366 --> 00:02:05,200
Regarding this PG signal,
27
00:02:05,566 --> 00:02:11,766
all PWM chips are open-drain outputs and need to be pulled up externally to high levels
28
00:02:16,533 --> 00:02:21,133
Here the PGND and phase pins are used for current detection
29
00:02:23,566 --> 00:02:31,233
BOOT pin is used for self-lift voltage and is externally connected to a self-lift voltage capacitor
30
00:02:38,933 --> 00:02:44,900
When we are repairing the PWM circuit, it is forbidden to remove the chip and add power
31
00:02:47,266 --> 00:02:53,700
If the PWM chip is removed, the G poles of the upper and lower tubes are in a suspended state
32
00:02:54,800 --> 00:02:58,033
In this case, power is strictly prohibited
33
00:03:01,333 --> 00:03:03,266
Since the chip is removed,
34
00:03:04,600 --> 00:03:10,433
the MOS tube will conduct itself after the upper and lower tube G poles are suspended
35
00:03:11,066 --> 00:03:18,100
If energized, the high level of the D pole of the upper tube will flow directly to the back end of the inductor,
36
00:03:19,700 --> 00:03:22,600
which will burn the back circuit of the inductor
37
00:03:26,800 --> 00:03:29,800
So we in the replacement of PWM chip,
38
00:03:31,266 --> 00:03:35,100
we can measure the ground value of the G poles of the upper and lower tubes
39
00:03:38,233 --> 00:03:42,900
If the ground value is infinite, the chip is not welded properly
40
00:03:45,033 --> 00:03:48,700
Ok, this is the workflow of a single PWM controller
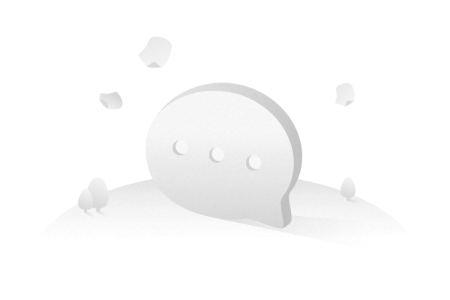