after the solder joints are teamed
we'll move the plastic connector from another C
model mutter board for this one
or by a new plastic connector from the market
and solder it back to the mutter board
before weld it back on the motherboard
we
first need to apply a layer of flux to the motherboard
when applying the solder
blow the motherboard a little with an air gun
make it a little warmer
in this way
the floss can be applied more evenly and thinner
if we don't warm it if with gloom temperature
after the flux is applied it may become a lump
which is not easy to spread
after the flux is applied
we put a pre
disassembled plastic connector on the motor board
positioning
our alignment
we just need to see if
this horizontal row of golden pins
and the silver white
solder joints at the bottom are aligned
just align it then take a closer look
are there any white dots under the first
row horizontally
are there any dots under the bottom row horizontally
likely to have this effect
some newbies may have this effect by accident
if so let's check the middle area
each pin is alliant
but there is an extra pin on the bottom
there is one more setter joint at this position
this is the common problem
it's called mall position
although the paints in the middle area are aligned
but look at the top of this
a lot of solder
the bottom side is quite different from the top
this is the mall position
we must completely match the solder joints
like when you loosen the tweezers
it is possible that the tweezered legs
will drive the connectors to move slightly
it's because there is a
little flux on the surface of the connector
it will stick to the tweezers
blow it with the hot air gun
then remove the tweezers and it won't move
the conductor
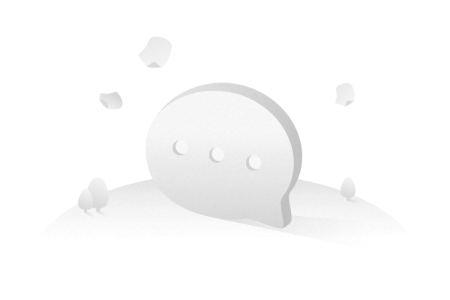