1
00:00:03,100 --> 00:00:05,900
Let's wait for the motherboard to cool down a bit
2
00:00:07,333 --> 00:00:10,300
Start cleaning the residual flux on the motherboard
3
00:00:13,700 --> 00:00:15,333
After soldering the connector
4
00:00:15,400 --> 00:00:19,200
There will be a lot of this flux on the motherboard.If you don't clean it
5
00:00:19,366 --> 00:00:23,766
It will lead to poor plugging and unplugging contact of the plastic connector
6
00:00:26,133 --> 00:00:27,566
You can clean it directly
7
00:00:28,466 --> 00:00:33,733
First, decompose the soldering oil and dilute it with PCB cleaner
8
00:00:41,800 --> 00:00:44,866
Then put a clean lint-free cloth on the surface
9
00:00:46,000 --> 00:00:47,200
Clean with cloth
10
00:01:04,300 --> 00:01:07,866
Use the other area of the dust-free cloth to clean again
11
00:01:09,733 --> 00:01:10,766
It'll be cleaner
12
00:01:24,133 --> 00:01:25,466
Now it's done
13
00:01:28,133 --> 00:01:33,333
Now we can observe whether there are individual pins in the solder joints that are not soldered
14
00:01:36,733 --> 00:01:42,466
Because sometimes there are some solder joints that you add solder, and the operation is not good
15
00:01:42,533 --> 00:01:47,966
Or there are some dirt residues on the pins of the solder joints that are not noticed
16
00:01:47,966 --> 00:01:51,633
It may cause individual pins to be loose and not welded on
17
00:01:51,833 --> 00:01:52,733
Let's take a look
18
00:01:52,900 --> 00:01:57,700
Mainly look at this edge, the extra space of these solder joints that are around the pins
19
00:02:01,000 --> 00:02:02,933
Everywhere becomes very flat
20
00:02:03,533 --> 00:02:04,866
This means no problem
21
00:02:05,133 --> 00:02:08,400
If the individual corners are very round and very full
22
00:02:08,500 --> 00:02:11,033
It is possible that it is not soldered on
23
00:02:11,100 --> 00:02:14,000
Now let's take a look at the top and bottom sides
24
00:02:14,000 --> 00:02:14,733
No problem
25
00:02:14,933 --> 00:02:17,500
If you suspect individual pins are loose
26
00:02:17,533 --> 00:02:20,166
You can use tweezers to push around like this
27
00:02:20,266 --> 00:02:22,200
If you find this pin is loose
28
00:02:22,300 --> 00:02:30,133
At this time, we can use the water-ingress corrosion plastic connector treatment method we learned in the previous lesson to operate
29
00:02:31,100 --> 00:02:33,300
Dip a little solder paste with tweezers
30
00:02:33,966 --> 00:02:37,133
Apply medium temperature solder paste to this solder joint
31
00:02:37,500 --> 00:02:39,100
Melt the solder by blowing
32
00:02:40,833 --> 00:02:43,566
After the solder paste is blown, wrap it up
33
00:02:43,566 --> 00:02:45,966
to achieve an effect of repeat welding
34
00:02:47,900 --> 00:02:49,033
If no loosening
35
00:02:49,966 --> 00:02:51,500
The welding is completed
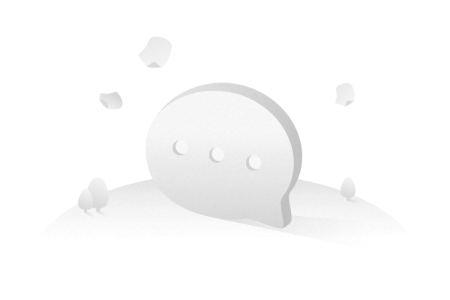