1
00:00:03,766 --> 00:00:06,100
Next we are ready to install it back
2
00:00:06,666 --> 00:00:07,900
Clean the pads first
3
00:00:15,000 --> 00:00:17,600
Before welding, first check pads
4
00:00:17,900 --> 00:00:21,466
Because when we scraped the glue, we scraped the copper exposed
5
00:00:21,600 --> 00:00:23,366
For example,like this pad
6
00:00:24,333 --> 00:00:25,800
It's a very rounded pad
7
00:00:26,066 --> 00:00:28,100
It has no connection to the periphery
8
00:00:28,866 --> 00:00:34,400
Once the edge of this position is exposed to copper, it must be replenished with green oil
9
00:00:34,466 --> 00:00:37,066
The one next to it, for example, like this
10
00:00:37,300 --> 00:00:40,333
Obviously we can see that it has four directions
11
00:00:40,600 --> 00:00:42,866
connected to the external ground wire
12
00:00:42,966 --> 00:00:43,966
This is grounded
13
00:00:44,300 --> 00:00:48,800
If there is exposed copper next to it, there is no need to fix it up
14
00:00:49,400 --> 00:00:51,866
Also, we see this kind of wired wiring
15
00:00:51,900 --> 00:00:53,300
These are useful pins
16
00:00:53,400 --> 00:00:58,033
Once there is copper exposed on the edge, it needs to be filled with green oil
17
00:00:58,533 --> 00:01:01,300
If you don't know where you need to fix up or not
18
00:01:01,666 --> 00:01:04,666
Just fix it up once you find any exposed copper
19
00:01:04,966 --> 00:01:06,533
This is the simplest way
20
00:01:07,266 --> 00:01:10,400
The other is to look at this area inside the component
21
00:01:12,733 --> 00:01:15,366
Is there any glue that has not been scraped off
22
00:01:16,466 --> 00:01:18,333
A little bit more like this area
23
00:01:18,833 --> 00:01:20,266
It's not cleaned enough
24
00:01:20,466 --> 00:01:21,933
We'll clean it up later
25
00:01:23,633 --> 00:01:26,300
Like this area which glue is not scraped clean
26
00:01:29,633 --> 00:01:31,133
We need to deal with it again
27
00:01:33,500 --> 00:01:35,866
A lot of this glue will affect our welding
28
00:01:42,800 --> 00:01:45,733
Also, this solder slag must be cleaned
29
00:01:46,566 --> 00:01:48,733
When we are flattening low melt solder
30
00:01:49,100 --> 00:01:53,900
It is possible that the capacitors or pins on the edge will get some low melt solder
31
00:01:56,166 --> 00:01:58,066
After getting some low melt solder
32
00:01:58,500 --> 00:02:00,600
It will protrude a little inwardly
33
00:02:00,766 --> 00:02:05,700
Then when we solder the chip, it may stick to the cross-section of the lateral edge of the chip
34
00:02:05,933 --> 00:02:07,266
Just like this position
35
00:02:07,700 --> 00:02:12,666
The pin of the capacitor must be grounded at one end and power supply at the other end
36
00:02:13,033 --> 00:02:18,466
The big ones next to the hard drive are grounded at one end and powered at the other end
37
00:02:18,933 --> 00:02:20,800
This silver part is grounded
38
00:02:20,966 --> 00:02:26,866
When we measure, sometimes the testing lead will be placed on the surface of the hard disk to measure
39
00:02:27,200 --> 00:02:29,600
The silver on this surface is all ground
40
00:02:29,733 --> 00:02:33,500
Once the solder on the edge of the capacitor touches the side of the chip
41
00:02:35,266 --> 00:02:37,966
The hard drive may short-circuit when installed
42
00:02:38,500 --> 00:02:44,300
For example, there is a lot of solder sticking in this position, and it touches the side of the hard disk
43
00:02:44,733 --> 00:02:47,100
It'll be find once the hard drive is removed
44
00:02:47,633 --> 00:02:50,566
It is found that there is no exposed copper position
45
00:02:50,833 --> 00:02:56,466
But as soon as you put it on, it's short-circuited, and when you take it off, it's fine
46
00:02:56,666 --> 00:02:58,933
The hard disk can be read in the test rack
47
00:02:59,200 --> 00:03:01,900
At this time, many people can't find the problem
48
00:03:02,100 --> 00:03:09,066
In fact, it is because the edge of the peripheral capacitor is stuck to too much solder, and the contact occurs
49
00:03:09,566 --> 00:03:13,966
There is still some glue residue on the edges that has not been completely cleaned
50
00:03:14,433 --> 00:03:16,300
We'll get a brush to clean it off
51
00:03:18,000 --> 00:03:20,433
And now the motherboard has been cleaned well
52
00:03:20,666 --> 00:03:22,333
Let's put a bit soldering oil
53
00:03:24,600 --> 00:03:26,600
Blow it a bit with a hot air gun
54
00:03:26,966 --> 00:03:31,200
The soldering oil applied on the board will be more uniform when the board is warm
55
00:03:31,466 --> 00:03:33,533
And the thickness will be appropriate
56
00:03:35,266 --> 00:03:38,500
When the board is not warm, it will be very thick
57
00:03:42,500 --> 00:03:44,800
All pads have been smeared with flux
58
00:03:45,433 --> 00:03:47,233
Then we start to weld the chip on it
59
00:03:47,833 --> 00:03:51,600
The position where I entered the blade just now is exactly the pin 1
60
00:03:53,100 --> 00:03:56,600
There is still a little scratch at this position where I entered the knife
61
00:03:57,566 --> 00:03:59,600
This is the place where I entered the knife
62
00:03:59,966 --> 00:04:02,800
We put this corner in the direction where I entered the knife
63
00:04:03,133 --> 00:04:04,733
In the top right direction
64
00:04:05,233 --> 00:04:06,900
This is where I entered the knife
65
00:04:07,700 --> 00:04:10,466
Just about this place and there is no exposed copper
66
00:04:10,966 --> 00:04:13,800
Some people are lazy and do not replenish green oil
67
00:04:14,033 --> 00:04:16,933
If you don't,then you have to put it very right
68
00:04:17,533 --> 00:04:20,533
After the chip is placed, we will start soldering
69
00:04:21,033 --> 00:04:24,933
Adjust the temperature to around 280-300 degrees
70
00:04:25,266 --> 00:04:27,733
Then turn the air volume to level 3-4
71
00:04:28,133 --> 00:04:32,233
When blowing, firstly blow the area where I enter the knife
72
00:04:32,500 --> 00:04:34,466
Blown to this place and collapsed
73
00:04:34,600 --> 00:04:36,533
And then blow to other places
74
00:04:40,833 --> 00:04:45,600
Whether it is disassembled or installed, it must be kept away from the CPU
75
00:04:57,233 --> 00:04:59,133
I've seen a bit of a collapse here
76
00:04:59,533 --> 00:05:01,200
Then we blow other positions
77
00:05:06,033 --> 00:05:08,566
I saw that the chip has a slight homing action
78
00:05:11,000 --> 00:05:13,033
If you can hold tweezers steady
79
00:05:13,466 --> 00:05:18,133
At this time, you can choose to use tweezers to gently push the chip on the corner
80
00:05:18,233 --> 00:05:20,500
Push it a little and it bounces back
81
00:05:20,866 --> 00:05:22,533
That means it's fully placed
82
00:05:22,933 --> 00:05:23,966
Do not press
83
00:05:24,266 --> 00:05:27,466
Push it from the side like this, don't press
84
00:05:28,133 --> 00:05:33,900
Because the pads of the hard disk are relatively loose, the middle spacing is relatively large
85
00:05:34,533 --> 00:05:35,833
You can try like this
86
00:05:36,300 --> 00:05:39,233
Small chips are not recommended to try like this way
87
00:05:39,333 --> 00:05:42,233
It is easy to short-circuit if you are not skilled
88
00:05:42,466 --> 00:05:44,266
Okay, we're done welding
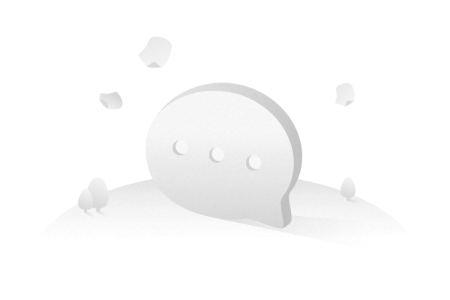