1
00:00:02,600 --> 00:00:06,866
Next, we start to remove the residual tin on the pads of the mainboard
2
00:00:09,200 --> 00:00:13,033
The glue on the bottom of the chip is basically taken away by the chip,
3
00:00:13,666 --> 00:00:15,133
when the chip is pried off
4
00:00:16,700 --> 00:00:19,533
Look, this is the the thick layer of black glue
5
00:00:21,466 --> 00:00:25,033
However, there is still a ring of glue on the edge of the mainboard.
6
00:00:25,700 --> 00:00:29,800
So we can directly apply the low melst solder to the mainboard when we flatten
7
00:00:30,500 --> 00:00:33,166
Because the surrounding glue forms a partition,
8
00:00:35,233 --> 00:00:38,466
The middle one is lower than the surrounding area, like a pool
9
00:00:39,400 --> 00:00:41,133
When you flatten the low melt solder,
10
00:00:41,366 --> 00:00:44,300
even if the low melt solder flows to the periphery,
11
00:00:44,666 --> 00:00:47,966
it is not easy to touch the small components on the edge
12
00:00:48,333 --> 00:00:51,366
Can add appropriate amount of low melt solder
13
00:00:54,900 --> 00:00:56,866
Add a small amount multiple times
14
00:00:57,200 --> 00:00:58,600
Let's add a little first,
15
00:00:59,200 --> 00:01:03,266
and if it's not enough to flatten on the edges, we'll add a little more
16
00:01:03,400 --> 00:01:04,733
Don't add too much at once
17
00:01:24,666 --> 00:01:28,966
Make sure that every pad around the perimeter is flattened by the soldering iron
18
00:01:49,333 --> 00:01:53,200
There is a piece of copper foil stuck on the tip of the soldering iron
19
00:01:56,700 --> 00:02:00,066
Let's wipe it off, otherwise, it might stick to these pads
20
00:02:00,933 --> 00:02:02,800
A little more low melt solder
21
00:02:12,933 --> 00:02:15,066
This pcb board is of poor quality,
22
00:02:17,866 --> 00:02:20,333
the soldering iron did not touch the board much,
23
00:02:20,333 --> 00:02:22,900
and a small part began to leak copper.
24
00:02:23,800 --> 00:02:27,766
Like this position, the color here has also become a little lighter.
25
00:02:28,500 --> 00:02:31,600
Therefore, we must pay attention to our strength when we flatten
26
00:02:32,133 --> 00:02:34,233
This board is very easy to leak copper
27
00:02:40,766 --> 00:02:44,200
The tin on the edges and corners is not easy to melt,
28
00:02:47,000 --> 00:02:50,300
just flatten the soldering iron back and forth at different angles
29
00:02:51,200 --> 00:02:53,400
to make sure it is completely melted
30
00:03:19,600 --> 00:03:24,366
This position was flattened a little more, and the copper foil leaked out a little bit.
31
00:03:24,700 --> 00:03:26,000
This board is so bad
32
00:03:59,733 --> 00:04:02,700
Okay, we're done with the low melt solder on the mainboard
33
00:04:03,000 --> 00:04:05,533
Now let's flatten the low melt solder on the chip.
34
00:04:08,633 --> 00:04:11,800
We use the chip card position on the fixture to fix the chip
35
00:04:14,466 --> 00:04:16,533
There is very little tin remaining on the chip,
36
00:04:16,700 --> 00:04:19,600
because the temperature of the chip we pry is very suitable
37
00:04:23,700 --> 00:04:26,800
There is still a lot of low melt solder on the soldering iron,
38
00:04:27,033 --> 00:04:28,466
we don't need to add more
39
00:04:39,666 --> 00:04:41,733
There is a thick layer of glue on the chip,
40
00:04:42,000 --> 00:04:44,433
which separates the soldering iron and the chip.
41
00:04:46,133 --> 00:04:49,066
So at this time, it doesn't matter if you flatten a little more
42
00:04:55,233 --> 00:04:57,066
Okay, we're done with the flattening
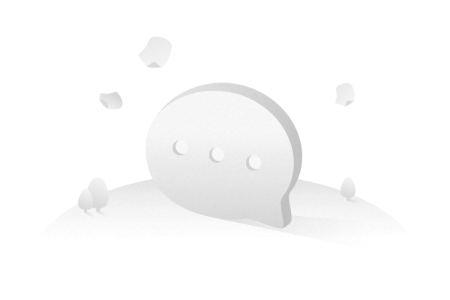