1
00:00:00,466 --> 00:00:04,700
Hello everyone, in this lesson we will talk about the soldering of EC chips
2
00:00:05,266 --> 00:00:08,066
Let's talk about the disassembly of the EC chip first.
3
00:00:08,566 --> 00:00:12,900
Before disassembling the EC, we need to apply a proper amount of flux to the pins of the EC
4
00:00:14,900 --> 00:00:19,200
After adding the flux, we need to use the air gun to heat the EC
5
00:00:21,200 --> 00:00:29,700
Here we need to pay attention to only heating the four side pins of the EC, not the EC itself
6
00:00:32,400 --> 00:00:35,200
The EC body is relatively fragile
7
00:00:35,366 --> 00:00:39,200
If heated for a long time, it may cause damage to EC
8
00:00:39,666 --> 00:00:44,200
We first use an air gun to blow and melt the applied flux
9
00:00:46,066 --> 00:00:53,300
After blowing and melting, use the corner of the tweezers to hold the corner of the EC
10
00:00:54,300 --> 00:01:02,033
Be careful not to pick up the tweezers, but to stuff them under the EC.
11
00:01:02,433 --> 00:01:13,700
If the tweezers are picked up all the time, it may cause the pins of the EC to be deformed or even the pads to fall off.
12
00:01:17,566 --> 00:01:26,266
We use an air gun with a temperature of 400 degrees and a wind speed of 60 to evenly heat the four sides of the EC
13
00:01:27,266 --> 00:01:34,533
When the pins on the four sides start to melt, the tweezers will continue to penetrate the bottom of the EC
14
00:01:35,400 --> 00:01:41,066
When the pins on all four sides are melted, we can use tweezers to remove the EC
15
00:01:43,000 --> 00:01:47,066
After removing the EC, we first need to clean the pads
16
00:01:48,366 --> 00:01:51,566
It can be seen that the current pad is uneven
17
00:01:52,766 --> 00:01:56,733
We use soldering iron and tin wire to drag solder the pad
18
00:01:57,100 --> 00:02:01,000
Note that the direction of drag welding must be along the pad
19
00:02:01,400 --> 00:02:05,700
If you don't follow the pad, it may drag the pad off
20
00:02:06,066 --> 00:02:10,700
After the EC pad falls off, it is very difficult to repair the pad
21
00:02:16,866 --> 00:02:20,766
After the pad is flattened, clean the pad
22
00:02:21,400 --> 00:02:24,966
After cleaning up, the processing of the pad is over
23
00:02:25,966 --> 00:02:29,000
Let's deal with the removed EC next.
24
00:02:30,066 --> 00:02:34,466
It can be seen that there are some glitches on the pins of this EC
25
00:02:34,933 --> 00:02:38,733
We need to drag these glitches out of it
26
00:02:40,166 --> 00:02:45,400
Of course, if you are using a new EC, you can skip this step directly
27
00:02:46,633 --> 00:02:50,133
We apply flux to the four pins of the EC
28
00:02:54,866 --> 00:03:00,633
Then use the knife side of the soldering iron to stick the residual tin on the pins
29
00:03:02,333 --> 00:03:07,333
When doing this step, be careful not to overdo it.
30
00:03:07,733 --> 00:03:12,166
If it is too heavy, it may bend the pins of the EC
31
00:03:13,166 --> 00:03:20,333
After cleaning the pins of the EC, the EC has completed the processing and entered the state of being soldered
32
00:03:21,966 --> 00:03:24,966
Next, let's look at the solder of EC
33
00:03:25,733 --> 00:03:31,100
You can see that there is a point on this position of the motherboard, which represents the first pin of the EC
34
00:03:31,400 --> 00:03:36,766
It can be seen that there is also a dot on the chip, which represents the first pin of the EC chip
35
00:03:36,933 --> 00:03:43,666
When soldering, be sure to match them up, otherwise the chip will be soldered upside down
36
00:03:44,200 --> 00:03:47,200
Next we need to align the EC
37
00:03:47,700 --> 00:03:50,200
The alignment of the EC must be very precise
38
00:03:50,400 --> 00:03:55,300
Even if the alignment is a little bit off, the subsequent drag welding will become very difficult
39
00:03:56,166 --> 00:03:59,333
After the position is correct, we first press and hold EC
40
00:04:00,133 --> 00:04:05,700
Use a soldering iron to add tin to some of the pins of the EC to fix the EC
41
00:04:09,933 --> 00:04:13,800
After the EC is fixed, you can let go
42
00:04:14,900 --> 00:04:18,800
Next we use a soldering iron to fill the sides with tin
43
00:04:19,933 --> 00:04:25,166
After filling up the tin, we are about to start drag soldering
44
00:04:25,300 --> 00:04:28,700
First rub the tip of the soldering iron back and forth on the pin
45
00:04:29,400 --> 00:04:32,100
This way the pins are not easy to solder
46
00:04:32,900 --> 00:04:39,666
You need to pay attention when rubbing, it must not be too big, otherwise it is easy to bend the pins
47
00:04:40,200 --> 00:04:44,800
Next we zigzag the pins with a soldering iron
48
00:04:45,266 --> 00:04:48,400
This can quickly bring the tin down
49
00:04:50,100 --> 00:04:58,333
Then we keep repeating the actions of dipping tin and wiping tin until all the tin on the pins is taken off
50
00:05:01,933 --> 00:05:07,966
At the end of soldering, there will always be a little solder that cannot be dragged down
51
00:05:09,000 --> 00:05:15,366
At this time, we can add some flux, and then tap it with the tip of the soldering iron, and it will come down
52
00:05:21,366 --> 00:05:24,400
This side has been mopped clean
53
00:05:24,800 --> 00:05:29,466
Then we drag the other 4 sides in turn.
54
00:05:31,600 --> 00:05:37,800
After cleaning, we need to check the EC to see if there is any empty soldering and linked soldering
55
00:05:38,733 --> 00:05:42,000
Linked soldering is easy to check, you can tell at a glance
56
00:05:42,366 --> 00:05:45,200
For empty soldering, we need to use tweezers to scrape
57
00:05:45,333 --> 00:05:47,266
Let's scrape next
58
00:06:07,000 --> 00:06:09,966
It can be seen that each pin is very firm
59
00:06:10,333 --> 00:06:13,933
Then the soldering of the EC is complete.
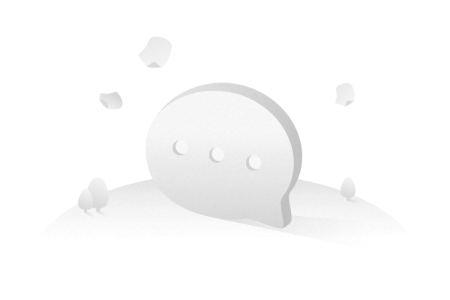