1
00:00:02,300 --> 00:00:08,166
When we repair this kind of double-layer mainboard, we rarely plant the solder on the middle frame
2
00:00:13,566 --> 00:00:17,233
Generally, after the mainboard is divided into layers,
3
00:00:17,233 --> 00:00:20,366
we go to find the internal faults of the mainboard
4
00:00:20,933 --> 00:00:25,966
After troubleshooting, we use a dedicated test stand to test the function
5
00:00:26,100 --> 00:00:31,766
After the function test is normal, we directly use the original solder to paste it back
6
00:00:32,500 --> 00:00:37,200
In this way, the solder points will be very stable and easy to paste
7
00:00:37,933 --> 00:00:41,366
I am now demonstrating to replant the solder
8
00:00:45,000 --> 00:00:50,433
To replant the solder, we need to level the residual solder on the middle frame
9
00:00:50,900 --> 00:00:53,833
We'd better operate on this heating table
10
00:00:56,933 --> 00:01:01,333
Because there is still some residual temperature on the heating table,
11
00:01:01,666 --> 00:01:07,400
in this way, the solder will be relatively easy to drag during the dragging process
12
00:01:14,900 --> 00:01:18,800
First add a little solder paste to the solder points
13
00:01:23,966 --> 00:01:29,966
Then use a soldering iron to match this suction line, and flatten all the solder points to it
14
00:01:55,900 --> 00:01:59,333
Why is the original solder paint easy to fit?
15
00:01:59,566 --> 00:02:05,466
Because a pad will be placed on this solder point, the pad can play a supporting role
16
00:02:12,666 --> 00:02:17,266
In the process of bonding, basically there will be no short circuit
17
00:02:17,833 --> 00:02:21,966
If the tin planting is not good, there may be a short circuit
18
00:02:22,966 --> 00:02:26,500
We can see that there are some solders on the solder suction line,
19
00:02:26,500 --> 00:02:30,133
similar to when we make glueless chips or CPUs
20
00:02:30,600 --> 00:02:35,166
When dragging the tin, the empty spot on the main board, the round metal piece,
21
00:02:35,166 --> 00:02:38,700
is basically the same size as this solder point.
22
00:02:41,966 --> 00:02:46,766
This is placed in the middle of the upper and lower layers to play a supporting role
23
00:02:47,266 --> 00:02:49,133
We glued this mainboard
24
00:02:49,466 --> 00:02:53,900
You can apply some pressure from above, it's not easy to short circuit
25
00:02:54,400 --> 00:03:00,166
However, if the size of the tin implants is uneven, or the solder points are relatively large,
26
00:03:00,166 --> 00:03:02,566
short circuits are prone to occur.
27
00:03:03,166 --> 00:03:09,700
Therefore, it is not recommended to replant tin unless there are some dropped spots on the upper mainboard.
28
00:03:14,800 --> 00:03:20,000
For example, if there is a drop point at this edge position, we will make up the point
29
00:03:20,533 --> 00:03:23,766
After finishing, there may be some unevenness
30
00:03:24,066 --> 00:03:27,400
We can drag the solder points down and re-solder
31
00:03:27,766 --> 00:03:32,166
Under normal circumstances, we generally do not replant tin
32
00:03:33,100 --> 00:03:36,466
I can't see clearly because I don't use a microscope
33
00:03:36,866 --> 00:03:41,300
There is that kind of small gasket dragged down from the solder suction line
34
00:03:41,566 --> 00:03:43,766
I don't know if it can be focused
35
00:03:44,200 --> 00:03:45,233
Have a look
36
00:04:11,100 --> 00:04:14,700
It is very easy to drag tin on this heating table
37
00:04:15,066 --> 00:04:20,500
Because there is residual heat at the bottom, there is no need to mop it very clean
38
00:04:57,566 --> 00:05:04,333
When we planting the tin, as long as the tin on the solder point is not too high, it doesn't matter
39
00:05:07,233 --> 00:05:11,333
In the process of dragging tin, pay attention to this aluminum block,
40
00:05:11,333 --> 00:05:16,200
be careful not to burn your hands, because it has more than 200 degrees
41
00:05:37,866 --> 00:05:41,866
Well, all the solder points are basically leveled out
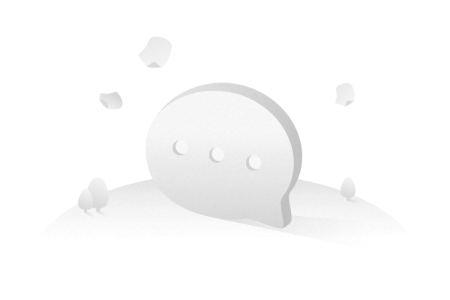