1
00:00:03,066 --> 00:00:08,933
Next, we find a scrapped iPhone mainboard and remove an inductance coil that has not been glued
2
00:00:13,100 --> 00:00:17,966
When dismantling, it is best to find the top where the pins cannot be seen
3
00:00:18,433 --> 00:00:22,833
It is best not to remove the inductor that has pins on both sides
4
00:00:23,333 --> 00:00:27,333
Remove the inductor that has pins welded on the mainboard
5
00:00:29,300 --> 00:00:34,066
Take a straight air gun and blow it at 450 degrees, while blowing,
6
00:00:34,533 --> 00:00:37,433
gently touch it with tweezers, don't force it
7
00:00:42,600 --> 00:00:45,866
When it comes loose, gently clamp it with a pinch
8
00:00:49,500 --> 00:00:55,200
Removing this inductance is used to tin the solder points on the main board of the plastic seat
9
00:00:57,700 --> 00:01:03,200
After the inductor is removed, let's check if the solder points have been broken off
10
00:01:05,966 --> 00:01:11,333
If you use too much force when disassembling, the solder points may be broken off
11
00:01:14,366 --> 00:01:17,533
Now the two solder points are still relatively bright,
12
00:01:17,533 --> 00:01:20,633
there is no problem with this, put it aside
13
00:01:21,900 --> 00:01:26,900
We take out the medium temperature solder of 183 degrees
14
00:01:39,266 --> 00:01:43,266
Pick up a small lump with tweezers and wipe it on the fixture
15
00:01:45,800 --> 00:01:50,466
Spread into two tin pieces of the same size and blow them with an air gun
16
00:02:04,100 --> 00:02:08,900
First use one of the legs of the inductor to connect to a piece of solder paste
17
00:02:13,266 --> 00:02:15,366
The temperature doesn't matter much,
18
00:02:15,366 --> 00:02:19,400
as long as the tin can be blown, the air gun doesn't matter
19
00:02:19,733 --> 00:02:24,300
A lump of it has been blown and stuck to the solder points of the inductor
20
00:02:24,766 --> 00:02:26,866
Reverse the inductance
21
00:02:32,300 --> 00:02:37,733
After blowing the two lumps of solder paste, stick to both sides of the solder point
22
00:02:38,266 --> 00:02:41,700
In this way, the inductor is already soldered
23
00:02:43,500 --> 00:02:45,266
Next we clean it
24
00:02:45,800 --> 00:02:50,233
Because there may be some broken tin slag on the edge of the inductor
25
00:02:50,966 --> 00:02:55,633
Let's use a brush dipped in board washing water to clean the tin slag
26
00:03:12,666 --> 00:03:15,500
Ok, so the inductor is tinned
27
00:03:22,400 --> 00:03:26,533
We put the inductor on top of the plastic seat that needs to be tinned,
28
00:03:26,900 --> 00:03:29,400
and then add a little more solder paste
29
00:03:33,500 --> 00:03:38,733
If the original solder paste on the mainboard is particularly dirty, clean it
30
00:03:39,366 --> 00:03:43,600
Now this one is not particularly dirty, so I didn't wash it
31
00:03:44,233 --> 00:03:51,733
Use the rotary air gun, adjust the temperature to the same as before, 330-340 degrees
32
00:03:52,200 --> 00:03:54,833
Then blow the tin on the inductor
33
00:03:55,666 --> 00:04:00,000
Block it with tweezers to prevent the inductor from being blown away
34
00:04:03,266 --> 00:04:07,200
Now that the solder is melted, take the tweezers and push it
35
00:04:28,666 --> 00:04:34,766
In this way, the solder on the plastic seat is ready, and it is very full and even
36
00:04:42,866 --> 00:04:46,666
This edge is a little tinned, let's fix that
37
00:04:50,700 --> 00:04:53,733
Cut off a small section of the tin-absorbing wire,
38
00:04:53,900 --> 00:04:56,833
and hold the tin-absorbing wire with tweezers
39
00:04:57,933 --> 00:05:02,433
Put a corner of the tin suction line to the position where the tin is connected,
40
00:05:02,433 --> 00:05:06,100
and then use an air gun to blow the solder and stick it away
41
00:05:26,633 --> 00:05:31,000
In this way, the position of the short circuit has been dealt with
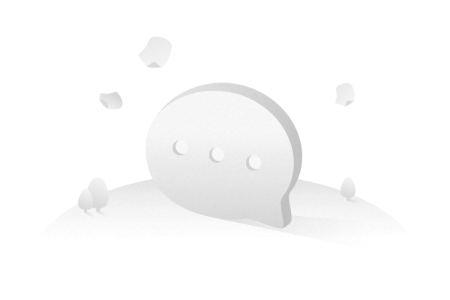