1
00:00:02,733 --> 00:00:05,233
Well, this seat has been welded
2
00:00:06,833 --> 00:00:12,733
Let's use tweezers to check the pin position of the plastic seat, whether it is fully connected
3
00:00:13,500 --> 00:00:17,133
Especially where the solder points are slightly fuller like this,
4
00:00:17,166 --> 00:00:20,233
be sure to touch them left and right with tweezers
5
00:00:20,800 --> 00:00:23,766
If it doesn't come loose, it's soldered on
6
00:00:25,433 --> 00:00:28,133
This side is closer to the glue
7
00:00:28,433 --> 00:00:31,633
Let's touch it with tweezers, it may loosen
8
00:00:33,466 --> 00:00:35,666
This pin is a little loose
9
00:00:36,900 --> 00:00:38,966
This place is also loose
10
00:00:39,500 --> 00:00:43,466
It may be that the piece of glue on the right has reached the seat
11
00:00:46,266 --> 00:00:48,833
Let's scratch the glue with tweezers
12
00:01:04,533 --> 00:01:08,466
Add some solder paste, solder after reheating,
13
00:01:54,700 --> 00:01:59,633
After melting, we wait for the mainboard to cool down a bit, then clean it
14
00:02:00,533 --> 00:02:05,633
If the plastic seat is not deformed, there is no dirt sticking to the bottom,
15
00:02:05,933 --> 00:02:09,400
and the solder points on the mainboard are relatively full,
16
00:02:09,500 --> 00:02:12,500
this kind of looseness will basically not occur
17
00:02:15,366 --> 00:02:19,400
Let's clean the mainboard now, first brush it with a brush
18
00:02:32,966 --> 00:02:37,666
Then put the dust-free cloth on it, wash it again through the dust-free cloth,
19
00:02:38,100 --> 00:02:42,166
and let the dust-free cloth take away these dirty things
20
00:02:55,400 --> 00:02:59,100
Then we observe the loose point at the magnification
21
00:02:59,566 --> 00:03:03,566
The first corner was loose just now, it is not loose now
22
00:03:04,666 --> 00:03:08,900
When we touch this pin, the glue in the middle does not respond
23
00:03:09,700 --> 00:03:12,500
There is basically no problem now
24
00:03:13,000 --> 00:03:15,500
Mainly observe the solder points
25
00:03:16,933 --> 00:03:23,433
If you see that the reflective intensity of any solder point is not the same as that of the surrounding area,
26
00:03:23,900 --> 00:03:26,466
you should touch it with tweezers
27
00:03:27,500 --> 00:03:30,833
Do not scratch hard to prevent short circuit
28
00:03:33,100 --> 00:03:35,266
Just push this pin lightly
29
00:03:36,166 --> 00:03:39,466
Each pin sticks out a little bit so you can see
30
00:03:46,066 --> 00:03:49,800
Be sure to pay attention when placing the mainboard,
31
00:03:50,533 --> 00:03:56,300
the leftmost pin and the rightmost pin correspond to gold-plated solder points
32
00:04:05,300 --> 00:04:08,633
If you are not careful, it may be misaligned,
33
00:04:09,000 --> 00:04:14,000
because the spacing between the solder points and the solder points is the same
34
00:04:14,500 --> 00:04:17,733
If one is wrong, there will be a wrong row
35
00:04:18,033 --> 00:04:24,533
So we must pay attention to whether the leftmost and rightmost two pins are aligned with the solder points
36
00:04:29,900 --> 00:04:35,200
When we solder, it doesn't matter a little bit to the left or a little bit to the right,
37
00:04:36,166 --> 00:04:40,900
as long as the first leg is not aligned with the second solder point
38
00:04:41,533 --> 00:04:44,233
Do not add too much when adding tin
39
00:04:44,666 --> 00:04:50,166
If the size of the tin addition is uneven, there is too much tin on the solder point,
40
00:04:50,533 --> 00:04:53,800
which may also cause the solder feet to connect together,
41
00:04:53,800 --> 00:04:57,866
just like the small components on the edge just connected together
42
00:04:58,300 --> 00:05:03,700
If there is connected tin, the processing method is the same as the method just now
43
00:05:04,900 --> 00:05:10,700
Take a small piece of tin suction line, and cut the front of the tin suction line a little bit sharper,
44
00:05:11,033 --> 00:05:15,400
because the distance between the solder points is relatively small
45
00:05:17,766 --> 00:05:22,200
Take the scissors at an angle, cut the tin suction line to a slanted point,
46
00:05:22,200 --> 00:05:26,733
and stuff the corner of the tin suction line between the two solder points
47
00:05:27,600 --> 00:05:33,733
If there is a short circuit, just plug it into this position and heat it up, and suck the tin away
48
00:05:37,866 --> 00:05:41,433
Ok, we have already welded the plastic seat
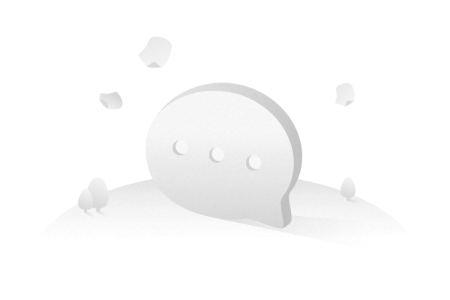